ECU1/ECU2 Series
Energy-Conservation Unit for Servopulser Hydraulic Power Supply Unit
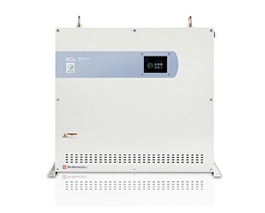
Energy-Conservation Unit
Up to 50 % energy savings. Contributes to reduced CO2 emissions and lower running costs. The conventional hydraulic power supply unit for fatigue and endurance tests is always driven at full power to achieve the maximum test force and maximum velocity and the hydraulic power supply unit is selected in order to satisfy the maximum test performance. Therefore, depending on the test conditions, energy is excessively consumed. With the ECU Series the motor rotational speed and the supply pressure of the hydraulic power supply unit can be set in multiple stages, so energy savings of up to about 50% can be achieved depending on the test conditions and test circumstances. It is used in combination with the Servo Controller 4830. (The Servo Controller 4830 is provided separately.) * Appearance and specifications are subject to change without notice.
Features
-
A conventional hydraulic power supply unit for fatigue and endurance testing machines runs continuously at full power to be able to generate the maximum test force and test speed...
-
The Eco Unit reduces the power from the hydraulic power supply unit according to the test conditions and circumstances to save energy.
The hydraulic power supply unit runs... -
Thsi tool simulates the reduction in running costs, such as power consumption, CO2 emissions using the ECU Series as compared to your servopulser hydraulic power supply unit.
Please click the banner for ecology...